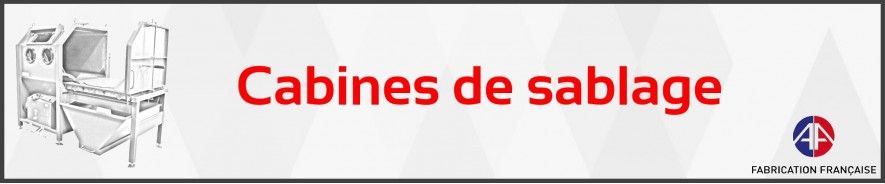
Sandblasting Booths
-
DF 700 - Sandblasting cabinet
The DF Expert Series Bag Cabsare the most advanced vacuummachines in our ranges.
The compact and high-performance ventilation system includes three modules to enable continuous dust removal and abrasive recycling, fine dust recovery and dust filtration.
This system offers greater working comfort for the user and preserves the components of the blasting cabinet.
(Price: contact us)
-
DC 700 - Sandblasting cabinet
The DC 700 handle blasting cabinet works very easily in a closed circuit.
The sprayed abrasive is vacuumed, sorted and then recycled. The dust is removed while the pure abrasive is recycled and reused for re-spraying.
All our equipment is designed and manufactured entirely in France in our factory in Marquette Lez Lille (59).
(Price: contact us)
-
DS 600 - Sandblasting cabinet
The DS600 vacuum blast cabinets, are reserved for very small parts and is a space-saving machine.
Its vacuum system projects the abrasive thanks to a venturi effect created inside the tungsten carbide nozzle .
The cyclone at the back of the blast cabinet is used to sort out the dust to be evacuated and the abrasive grains that can be reused.
(Price: contact us)
-
DF 1000 - Sandblasting cabinet
The Expert DF Series Bag Cabsare the most advanced vacuummachines in our ranges.
The compact and high-performance ventilation system includes three modules to enable continuous dust removal and abrasive recycling, fine dust recovery and dust filtration.
This system offers greater working comfort for the user and preserves the components of the blasting cabinet.
(Price: contact us)
-
DC 1000 - Sandblasting cabinet
The DC 1000 sandblasting booth has a very simple operation.
The sprayed abrasive is vacuumed, sorted and then recycled. The waste is discharged and the pure abrasive is recycled to be resprayed by the machine's tungsten carbide nozzle.
All our equipment is designed and manufactured entirely in France in our factory in Marquette Lez Lille (59).
(Price: contact us)
-
DS 700 - Sandblasting cabinet
The DS vacuum bag cabins use the same principle as all vacuum machines: a venturi system inside the tungsten carbide nozzle is used to project the abrasive onto the sandblasted workpiece.
The healthy abrasive is then separated from the dust in the cyclone at the back of the blast cabinet. The dust is collected in the collection bag and the abrasive is redirected to the nozzle.
(Price: contact us)
-
DS 1000 - Sandblasting cabinet
DS type bag cabins are professional sandblasting machines operating with a vacuum system. That is, the abrasive is projected via a venturi effect created inside the tungsten carbide nozzle .
The cyclone at the rear of the PRO series machines allows the abrasive to be sorted. Dust is discharged into the dust bag at the back of the sandblaster while larger grains of abrasive are reused.
(Price: contact us)
-
DF 1250 - Sandblasting cabinet
The Expert DF Series Bag Cabsare the most advanced vacuummachines in our ranges.
The compact and high-performance ventilation system includes three modules to enable continuous dust removal and abrasive recycling, fine dust recovery and dust filtration.
This system offers greater working comfort for the user and preserves the components of the blasting cabinet.
(Price: contact us)
-
DC 1500 - Sandblasting cabinet
The DC 1500 Sandblasting cabinet is suitable for larger workpieces.
The operating principle and handling remain the same as in the smaller cabinets: the sprayed abrasive is sucked up, sorted and then recycled.
All our equipment is designed and manufactured entirely in France in our factory in Marquette Lez Lille (59).
(Price: contact us)
-
DS 1500 - Sandblasting cabinet
The DS1500 sandblasting machines are the largest machines in the PRO range.
The operating mode of these cabins is the same as for the other DS type machines: the abrasive is projected thanks to the venturi system of the tungsten carbide nozzle .
It is then separated from the dust; The dust is discharged into the recovery system integrated into the baghouse, and the pure abrasive is recycled and reinjected into the nozzle.
(Price: contact us)
-
DC 600 - Sandblasting cabinet
The DC 600 sandblasting cabinet works very easily in a closed circuit.
The sprayed abrasive is vacuumed, sorted and then recycled. The dust is removed while the pure abrasive is recycled and reused for re-spraying.
All our equipment is designed and manufactured entirely in France in our factory in Marquette Lez Lille (59).
(Price: contact us)
-
DF 1500 - Sandblasting cabinet
The Expert DF Series Bag Cabsare the most advanced vacuummachines in our ranges.
The compact and high-performance ventilation system includes three modules to enable continuous dust removal and abrasive recycling, fine dust recovery and dust filtration.
This system offers greater working comfort for the user and preserves the components of the blasting cabinet.
(Price: contact us)
-
PS 700 - Sandblasting cabinet
The PS 700 blast cabinet combines the small footprint advantage with the productivity of a pressure boosting machine. The overpressure blasting means that the abrasive tank is pressurized and offers a 3 to 5 times higher yield compared to the vacuum.
Equipped with a cyclone, these sandblasting machines can sort the abrasive in order to separate dust and healthy abrasive grains. These are then reprojected.
(Price: contact us)
-
PF 700 - Sandblasting cabinet
The PF700 professional bag blasting cabinets combine performance with a small footprint.
They are recommended for parts that do not exceed 50cm and/or need to be difficult to pickle.
Pressure booths work with a simple principle; The abrasive tank is pressurized and the abrasive is projected through the boron carbide nozzle thanks to this principle.
At the back of the machine, two cyclones are responsible for sorting the abrasive and dust.
(Price: contact us)
-
PS 1000 - Sandblasting cabinet
The PS 1000 combines the small footprint advantage with the productivity of a pressure boosting machine. The overpressure blasting means that the abrasive tank is pressurized and offers a 3 to 5 times higher yield compared to the vacuum.
Equipped with a cyclone at the rear of the machine, the PRO range allows the abrasive to be sorted. Dust is discharged into the dust bag at the back of the sandblaster while larger grains of abrasive are reused.
(Price: contact us)
-
PF 1000 - Sandblasting cabinet
The PF type sleeve cabins are definitely the most powerful cabins in our range; They combine the quality of the materials and the pressure system for great sandblasting power.
Recommended for tough processing or for greater productivity, they can be equipped with the double pot option for continuous blasting without the need to stop to fill the abrasive tank.
(Price: contact us)
-
PS 1500 - Sandblasting cabinet
The PS1500 works with an abrasive tank that is pressurized for blasting with 3 to 5 times higher yields compared to the vacuum system.
The recycling cyclone allows the separation of dust from the abrasive. The waste is then discharged into the dust collection bags and the recycled abrasive is resprayed.
(Price: contact us)
-
PF 1250 - Sandblasting cabinet
The PF1250 professional blasting cabinets are "square" cabinets. Indeed, this model of machine is as wide as it is deep.
They allow the treatment of large parts in the sandblasting chamber and can strip any type of paint thanks to the overpressure spraying system.
The abrasive tank is pressurized and the abrasive is sent to the nozzle with the pressure build-up. This system allows for 3 times more efficiency than vacuum machines.
(Price: contact us)
-
PF 1500 - Sandblasting cabinet
The PF1500 blast cabinets make it possible to blast and strip larger parts.
The high-performance ventilation integrated into the cab and the two cyclones at the rear of the machine allow for a very good view of the blast chamber. They are also used to separate the healthy abrasive from the worn abrasive and dust to preserve the elements of the blasting machine.
The abrasive overpressure spraying system gets rid of the most stubborn paints.
(Price: contact us)
-
PF 1515E - Sandblasting cabinet
The 1515E bag cabinets are the largest blasting cabinets we offer in standard sizes. With their internal dimensions of 1.5x1.5x1 m, they make it possible to process large one-piece parts while maintaining the characteristics of our baghouses.
On this machine, the abrasive is projected thanks to its pressurized tank. The abrasive is sprayed and then recycled.
This machine from our EXPERT range, designed for intensive use, benefits from 2 cyclones at the rear of the cab, efficient ventilation, and a powerful engine.
Machine equipped with a reinforced loading trolley with turning table (CHAR3) and additionnal dust collector (DPE 750)
(Price: contact us)
What equipment is essential to operate a sandblasting cabinet?
At ARENA, we want to make our sandblasting solutions accessible to everyone. To individuals as well as to industrialists, to craftsmen as well as to multinationals; Our machines require a 220 volt single-phase power supply.
To supply compressed air, all our bag cabins need a compressor. The consumption of the blast cabinet depends on the abrasive blasting mechanism.
How is the abrasive sprayed?
There are 2 different means of projection in the bag booths in our range:
Vacuum machines, otherwise known as suction machines, are equipped with a venturi process gun that allows the abrasive to be sucked up from the tank and projected through a nozzle, it is a technically simple and economical system. In our baghouse the vacuum machines are those starting with the letter D: DC, DS, DF.
Pressure (or overpressure) machines incorporate a tank containing the sandblasting media which is pressurized in order to expel the abrasive through a lance ending in a nozzle, the pressure blasting system has an efficiency 2 to 3 times higher than the vacuum system, but it is technically more complex. Our pressure booths are type PS and PF booths.
The means of projection and the frequency of use are closely linked.
The different ranges of ARENA sandblasting cabinets
We have established our 3 ranges according to the optimal frequency of use of the machines:
The ECO range has been designed for occasional use of sleeve cabs. It is suitable for any type of surface treatment.
The machines in our PRO range have been designed for a standard use of sandblasting equipment of approximately 2 hours per day. This range includes a type of vacuum blaster, the DS machines, and an overpressure type, the PS.
The machines in the EXPERT range are the most sophisticated and are the ones with high-quality components. There are also vacuum machines, DF, and pressure booster machines, PF, in this range.
The ranges are physically differentiated by the different paints of the booths depending on the range but also and especially on the back of the booth.
The DC cabs in our ECO range have only one block at the rear of the machine. It includes the filter cartridge which is intended to retain dust and impurities before they fall into the dust collection bag just below.
PRO machines have an additional module on the back. This is an abrasive recycling cyclone. It is used to keep and reinject healthy abrasive grains into the nozzle for reuse.
The EXPERT range has a third element on the back of its machines: a second dust recycling cyclone which serves to protect the turbine and maintain a healthy and dust-free blasting atmosphere.
What about abrasives? / What are the abrasives to be used in sandblasting?
As far as sandblasting agents are concerned, all our machines can spray any type of abrasive! The only limit is the one imposed by the nozzle diameter of your machine. In general, it is customary to consider that a nozzle will only be compatible with grains less than a quarter of its internal diameter (nozzle of 4 mm = grains less than 1 mm)
As our bag cabinets benefit from an abrasive recycling system, recyclable abrasives are recommended for use in the blasting cabinet. Recyclable abrasives are ideal for use in the blast booth and can be sprayed several times before breaking and turning into unusable dust.
These abrasives can be made of a wide variety of materials, including: minerals, glass, metal, plastic, ceramics, etc.
Each material and form of abrasive has its own technical characteristics and strengths depending on the desired processing.
There are 3 main types of abrasives:
Angular abrasives tear material off the surface of parts. They are perfect for deburring, stripping, deoxidizing, etching or creating roughness.
Spherical abrasives such as microbeads (glass or ceramic) are generally used for cleaning, renovating or satin-finishing. They are often used on clean parts to give a clean and homogeneous finish state, whether on an entire part or on welds for example. Thanks to their round shape, these balls create a smooth surface finish on all metal parts.
The third type of abrasive is scrubbing abrasives. Usually made of plastic or vegetable material, they do not attack the surface of the room. They are mainly used to clean or treat delicate parts.
What sizes of sandblasting machine?
Our sandblasting cabinets are as versatile as possible; Our standard cabs benefit from a wide range of different sizes, often available from stock, ranging from 600 to 1500 mm wide.
We generally recommend that there is sufficient room between the size of the room and the size of the booth so that the room can be handled inside the booth easily. Most of the time, we estimate between 10 and 20 cm of spacing around the room to be able to handle it easily.
In the case of special dimensions, we can make sandblasting cabinets of any size, contact us to find out more about the possibilities!
A few words about us
Manufacturers of machines in the north of France for more than 40 years, we monitor spare parts over several years and have the right parts for each machine in stock in our premises. We ensure a response to any request within 24 hours maximum and availability of spare parts with delivery within 48 to 72 hours.
Do not hesitate to contact us for any sandblasting project. Our team of experts will certainly be able to provide you with information.
We are available by phone, email or via the contact tab.
You can also follow our news on our LinkedIn or YouTube networks.