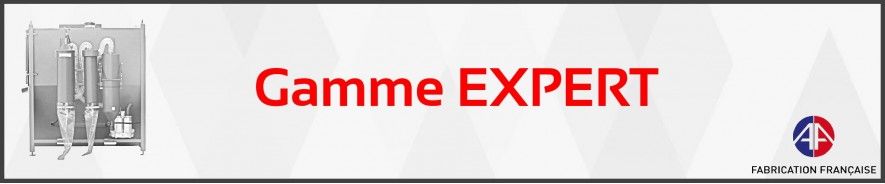
EXPERT range
-
DF 1000 - Sandblasting cabinet
The Expert DF Series Bag Cabsare the most advanced vacuummachines in our ranges.
The compact and high-performance ventilation system includes three modules to enable continuous dust removal and abrasive recycling, fine dust recovery and dust filtration.
This system offers greater working comfort for the user and preserves the components of the blasting cabinet.
(Price: contact us)
-
DF 1250 - Sandblasting cabinet
The Expert DF Series Bag Cabsare the most advanced vacuummachines in our ranges.
The compact and high-performance ventilation system includes three modules to enable continuous dust removal and abrasive recycling, fine dust recovery and dust filtration.
This system offers greater working comfort for the user and preserves the components of the blasting cabinet.
(Price: contact us)
-
DF 1500 - Sandblasting cabinet
The Expert DF Series Bag Cabsare the most advanced vacuummachines in our ranges.
The compact and high-performance ventilation system includes three modules to enable continuous dust removal and abrasive recycling, fine dust recovery and dust filtration.
This system offers greater working comfort for the user and preserves the components of the blasting cabinet.
(Price: contact us)
-
DF 700 - Sandblasting cabinet
The DF Expert Series Bag Cabsare the most advanced vacuummachines in our ranges.
The compact and high-performance ventilation system includes three modules to enable continuous dust removal and abrasive recycling, fine dust recovery and dust filtration.
This system offers greater working comfort for the user and preserves the components of the blasting cabinet.
(Price: contact us)
-
PF 1000 - Sandblasting cabinet
The PF type sleeve cabins are definitely the most powerful cabins in our range; They combine the quality of the materials and the pressure system for great sandblasting power.
Recommended for tough processing or for greater productivity, they can be equipped with the double pot option for continuous blasting without the need to stop to fill the abrasive tank.
(Price: contact us)
-
PF 1250 - Sandblasting cabinet
The PF1250 professional blasting cabinets are "square" cabinets. Indeed, this model of machine is as wide as it is deep.
They allow the treatment of large parts in the sandblasting chamber and can strip any type of paint thanks to the overpressure spraying system.
The abrasive tank is pressurized and the abrasive is sent to the nozzle with the pressure build-up. This system allows for 3 times more efficiency than vacuum machines.
(Price: contact us)
-
PF 1500 - Sandblasting cabinet
The PF1500 blast cabinets make it possible to blast and strip larger parts.
The high-performance ventilation integrated into the cab and the two cyclones at the rear of the machine allow for a very good view of the blast chamber. They are also used to separate the healthy abrasive from the worn abrasive and dust to preserve the elements of the blasting machine.
The abrasive overpressure spraying system gets rid of the most stubborn paints.
(Price: contact us)
-
PF 1515E - Sandblasting cabinet
The 1515E bag cabinets are the largest blasting cabinets we offer in standard sizes. With their internal dimensions of 1.5x1.5x1 m, they make it possible to process large one-piece parts while maintaining the characteristics of our baghouses.
On this machine, the abrasive is projected thanks to its pressurized tank. The abrasive is sprayed and then recycled.
This machine from our EXPERT range, designed for intensive use, benefits from 2 cyclones at the rear of the cab, efficient ventilation, and a powerful engine.
Machine equipped with a reinforced loading trolley with turning table (CHAR3) and additionnal dust collector (DPE 750)
(Price: contact us)
-
PF 700 - Sandblasting cabinet
The PF700 professional bag blasting cabinets combine performance with a small footprint.
They are recommended for parts that do not exceed 50cm and/or need to be difficult to pickle.
Pressure booths work with a simple principle; The abrasive tank is pressurized and the abrasive is projected through the boron carbide nozzle thanks to this principle.
At the back of the machine, two cyclones are responsible for sorting the abrasive and dust.
(Price: contact us)
How does the EXPERT range work?
The cabs in our EXPERT range are the most advanced of our sleeve cabs. They combine quality materials with an advanced sandblasting system.
The blasted abrasive is sucked up by the high-performance suction system in our bag cabs. Healthy abrasive, dust and dusty air are sucked up to the rear of the cab. At the rear of the cabin: 3 different modules including 2 recycling cyclones.
The purpose of the first cyclone is to separate the reusable abrasive from the dust and the spent abrasive grains. It is adjustable according to the abrasive particle size and a sieve retains the largest impurities. The cleaned abrasive can then be redistributed to the nozzle.
The dust and the spent abrasive grains are sucked up to the second cyclone where the heavier dust falls into the collection bag at the bottom of the cyclone at the back of the machine. The remaining fine dust is therefore stopped by this second cyclone and retained in the bag until the bag is evacuated.
The third block consists of the filter cartridge which aims to retain the last impurities, allowing clean and dust-free air to be released into the workshop.
The booths of the EXPERT range are divided into 2 categories, related to their means of projection.
There are vacuum cabins, DF type machines,
And the booster machines, the PF booths.
Vacuum booths project the abrasive via a venturi system created inside the nozzle. The abrasive is sucked in from the abrasive tank and is blasted through the nozzle via this vacuum system, otherwise known as a suction system.
Pressurized sandblasting machines expel the abrasive through the nozzle through the pressurized abrasive tank. Pressing the pedal of the machine releases the pressure and the abrasive is projected through the nozzle towards the workpiece to be sanded.
Processing a part in a handle booth with a pressure blasting mechanism is 2 to 3 times faster than a vacuum machine, but it is more complex and expensive to perform. Vacuum machines benefit from the most common system in sandblasting, it is a simple and inexpensive mechanism.
Regardless of the means of spraying, a sandblasting booth needs a tool that provides compressed air.
Which compressor for an EXPERT sandblasting machine?
All sandblasting machines need a compressor that will distribute the compressed air necessary for the proper functioning of the machine. However, not all machines need the same compressor.
The power required by the compressor depends initially on the means of projection; Booster cabins have a higher need for compressed air than vacuum machines.
The second point that is influenced by the power of the compressor is the nozzle diameter. Indeed, the larger the diameter of the nozzle, the more air will be needed to project the abrasive.
Do not hesitate to take a look at the technical sheets of the DF and PF cabins, all the information on the power of the compressor is detailed.
Which abrasive is suitable for these blast cabinets?
All recyclable abrasives are designed to be used in a bag cab and to be sprayed several times before breaking.
All types of recyclable abrasives are accepted in our bag cabins. There are 3 main types:
Angular abrasives such as brown corundum, for example, are well known because they are the same abrasive as on sandpapers. These are the most aggressive abrasives; They are perfect for stripping metal parts for example. There is also white corundum, different from brown corundum in its color; White corundum is simply brown corundum from which the iron oxide has been removed. This makes it possible to sand parts such as aluminium without the risk of rusting it, for example.
The second most well-known type of abrasive is spherical abrasive. Generally, microbeads are made of glass, but there are also ceramic or metal microbeads; The latter two are more resistant over time but are more expensive to buy.
Spherical abrasives are ideal for finishing a part. Their round shape allows for a clean and smooth finish.
Caution: in the case of glass microbeads, too intensive reuse would lead to the microbeads being broken and transformed into angular glass. Their effect would then be closer to the angular abrasive than to the spherical abrasive.
The third abrasives are those of scrubbing; This involves cleaning parts or treating fragile parts, often made of plastic. Gum abrasives such as plastic media allow you to clean any type of part without attacking the surface.
In general, it is said that a grain of abrasive should not exceed a quarter of the diameter of the nozzle. For example, for a 4 mm nozzle, the maximum grain size that can be sprayed correctly is 1 mm.
And after the purchase?
Present in the north of France for more than 40 years, we keep spare parts and consumables in stock in our premises.
Lots of glass (VI1), filter cartridges (CA8), gloves (CMV1 or CMV2) and abrasives are available all year round at ARENA and we deliver to you within 24 to 48 hours all year round!
Our technical teams can be reached by phone for any questions about your cabin or installation.
Don't hesitate to call them, they will certainly be able to answer you.
A few words about us:
Manufacturers of sandblasting machines in the north of France for more than 40 years, contact us for any questions about sandblasting; Our team of experts will certainly be able to inform you.
We also carry out tests on your parts in order to best estimate the machine and abrasives that best meet your needs.
We are available by phone, email or via the contact tab.
You can also follow our news on our LinkedIn or YouTube networks.