Sandblasting Booth
Over the years, Arena Blast has seen its catalog of sandblasting cabinets growing to meet the needs of professionals and industrialists.
As a provider of sandblasting and surface treatment solutions for more than 40 years, Arena Blast is the best company to meet with in order to find the most suitable sandblasting cabinets for your application!
What types of blast cabinets are available at Arena Blast?
First of all, it is important to know that sandblasting booths can be equipped with two abrasive blasting systems for different uses depending on the case;
Vaccum blasting system
Easy to use with easy adjustments and maintenance, this system uses the Venturi effect and is ideal for sandblasting cabinet applications without the need for high intensity. It is a less expensive system than overpressure.
In addition, it is possible to connect several blast nozzles to the same abrasive tank to increase the surface treatment capabilities of the sand box tenfold.
Pressure sandblasting system
For the pressure blasting cabinet, the abrasive is projected from the tank, which is pressurized by the sandblaster's compressor.
This system allows abrasive spray rates to be significantly higher than the vacuum.
With more efficient, intense and powerful use, it offers 3 to 5 times higher yields.
Discover our sandblasting booths
Details of our different models of sandblasting cabinets
Arena Blast offers 4 ranges of sandblasting machines for the different needs and uses you may have in terms of sandblasting solutions;
What is a sandblasting cabinet?
A sandblasting cabinet is a piece of equipment designed specifically to carry out sandblasting work with precision and safety. Unlike a mobile free-jet sandblaster, the sandblasting cabinet allows you to operate in a closed and controlled environment. The sandblasting cabinet can be installed in a small room indoors and allows work to be carried out with a neat finish.
Resembling a large box or an equipped box, the blast cabinet includes various essential elements;
The working chamber is the closed and totally airtight space in which the operator can carry out his sandblasting operations. This chamber is designed to be resistant to abrasive splashes and last over time
The sleeved gloves that are integrated into the sandblasting machine allow the operator to handle the parts in the cab without being in direct contact with the abrasive used
The viewing window, often made of glass or reinforced material, provides a clear view from the inside for the operator using the blast cabinet. The latter does not need to be very large because the operator will necessarily have to be in front of the window to be able to process the parts manually with the gloves. In addition, a small window will be easier to change when it becomes opaque due to the bounce of abrasives on the glass
The internal lighting of the cab guarantees optimal visibility during handling and sandblasting operations
The system for extracting the air/abrasive/dust flows that the sandblasting generates within the closed space. The machine is equipped with a side channel turbine allowing suction and making the booth environment depressurised.
The abrasive collector that collects used abrasive. This abrasive is then sorted and can be reused later to reduce costs and increase blasting accuracy
Numerous accessories for sandblasting cabinets allow manufacturers to adapt the sandblasting cabinet to their current needs and uses.
What are the uses for a sandblasting cabinet?
Sandblasting cabinets are used and widespread in many industries to clean, strip, prepare or restore surfaces. Here are some common examples of how our blast cabinets are used;
Industrial Cleaning & Stripping - To remove residues, oxidation or rust, stubborn impurities and other dusts to obtain clean parts before an industrial process
Sheet metal - preparation of metals by creating, by sandblasting, a surface roughness that will allow a better adhesion of the paint
Automotive & Aerospace - To strip mechanical parts prior to repair or mechanical work or to enable a painting operation
Precision Work - For working on delicate or small objects or parts that require careful work such as jewelry or electronic parts
Biomedical - surface finish by micro-bead blasting with glass or ceramic beads to have clean finishes to obtain satin surfaces
Antique Restoration - To strip metal parts, tools, decorative accessories, or any other antique object that has been affected by time
Sandblasting cabinets will be suitable for small workshops of expert craftsmen as well as for large industries requiring the stripping and cleaning of industrial parts. Whether you are an industrialist, mechanic, jeweler, restorer of old objects, etc., the sandblasting booth becomes an essential to allow you to save time and quality work.
How does a sandblasting booth work?
The principle of a sandblasting booth is simple and is based on an ingenious system combining efficiency, precision and safety. Here are the steps in the process of operating a sandblasting cabinet;
The first step is to load the cabin, i.e. install the object(s) to be sanded in the cabin. The operator therefore adds the object to be treated inside the working chamber of the blast cabinet.
The working chamber is designed to withstand repeated abrasive impacts in order, among other things, to protect the external environment of the machine from abrasive projection.
The object can then be positioned on a grid or on a rotating platform (turntable) depending on the model and options of the blasting cabinet.
The operator must then load the machine with abrasive (there are several types for a wide variety of applications). To do this, he pours a quantity of less than 8 liters inside the booth so that the abrasive is sucked into the bottom of the hopper.
Once the booth is closed, the user only has to use the glove sleeves to handle and intervene on the workpiece. The robust gloves are attached to the cab and make the machine completely secure. This means that the user is outside the cab and protected from abrasive and dust splashes.
The heart of the process takes place when the abrasive is sprayed into the cab. Indeed, it is at this moment that the sandblasting gun, which is connected to an air compressor, propels the abrasive at very high speed on the surface of the object in order to scrub it.
The operator then has full control over the blast gun which he directs through the sleeved gloves to precisely reach the areas to be treated.
The abrasive that is used can then vary, mainly depending on the nature of the work and the material on which the operator has to act; For example, coarse granules can be used to strip thick layers such as rust or stubborn paint, while finer particles allow for more delicate finishes such as cleaning metal parts or matting glass.
At the end of the blasting process, the abrasive is not removed and its residues will fall directly to the bottom of the hopper under the work grate of the blasting cabinet. The filter unit then sorts the used abrasive, removing unusable particles (paint, rust, etc.) and keeps the abrasive in good condition.
This is one of the main advantages of the sandblasting cabinet, which allows the recovery and reuse of the abrasive. This system allows operating savings but is also a gesture in favor of the ecology and the planet.
The blast cabinet is equipped with powerful internal lighting and a high-performance, compact and integrated suction and ventilation system with a triple module and a side channel impeller at the rear of the cabinet that quickly removes sandblast dust.
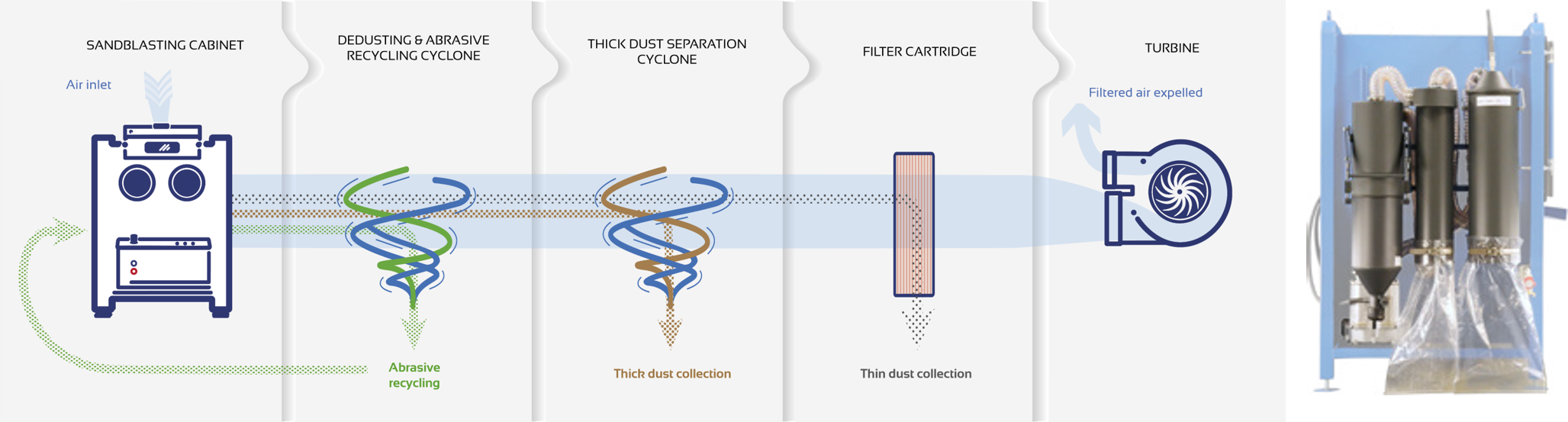
This device allows the cabin chamber to have maximum visibility to facilitate the operator's work.
The blast cabinet is designed to provide a fully controlled environment. It guarantees:
Precision thanks to abrasive jet containment
Safety by isolating the operator from residues and spatter
Savings thanks to abrasive recycling
In summary, a sandblasting cabinet turns sandblasting into a simple, efficient and environmentally friendly process.
Maintenance and servicing of your sandblasting cabinet
Arena Blast, as a manufacturer and distributor of sandblasting cabinets, offers you the supply of 100% of the spare parts for your future sandblasting cabinet to enable you to repair, maintain and maintain the sandblasting machine over time.
Our sandblasting cabinets are designed so that the replacement of wear elements (gloves, windows, filters, nozzles, gun, etc.) can be done quickly and intuitively so that you do not have to call in a specialist for small, routine maintenance.
The machines are multiple settings and allow you to adapt the sandblasting cabinet to your needs, for example;
The pressure gauge for adjusting the sandblasting pressure which allows an intensity from 0 to 8 bar
Another pressure gauge allows the adjustment of the filter cleaning pressure on our EXPERT range
The airflow that is adapted to the abrasive particle size to facilitate abrasive/dust separation
The machine height which is adjustable and adaptable according to the needs and environment
Also discover our other sandblasting machines
For more information: please contact us