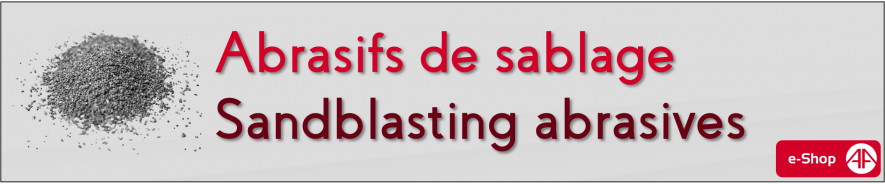
Abrasives for sandblasting
-
Almandine GARNET
€29.75 HTGARNET blasting abrasive, used for surface treatment operations by impact as well as for water jet cutting.
-
Aluminum Silicate
€16.75 HTAbrasive for free-blast blasting and soft stripping with mobile sandblasters or airbrushes.
Ideal for replacing SCOREX® SC250 (fine grid).
-
Angular Glass
€43.75 HTAngular abrasive made from recycled soda-lime-silica glass, which is ground and sieved to produce particles with angular edges. The particles have sharp edges, making them effective for polishing and cleaning.
-
Archifine Sand N°4 (25kg)
Archifine Sandblasting Sand N°4, the 25kg bag
Product unavailable; See the SCOREX SC250 article for equivalent abrasive.
-
-
Brown Corundum - ABC
€99.75 HTA tough, angular, mineral blasting abrasive ideally suited to stripping metal parts.
This very hard aluminum oxide can be blasted many times, and is widely recommended for use in bag blast cabinets.
-
Calcium silicate - SCOREX®
€16.75 HTAbrasive for free-blast sandblasting and stripping with mobile sandblasters
-
Ceramic Microbeads
€72.25 HTCeramic microbeads are one of the best choices when it comes to bead blasting. They offer superior strength to glass microbeads and require reasonable projection power due to their lightness.
They are made of very resistant zirconia oxide and do not contain iron, which allows the processing of stainless steel and aluminum.
The ceramic microbead is a guarantee of durability and efficiency.
-
Glass bead
€87.50 HTGlass microbeads are a precision blasting media for damage-free cleaning, maintaining tolerances, and are also suitable for deburring and satin finishing applications on metal parts made of aluminum, brass, or stainless steel. Their chemical inertness (insolubility in water or oil) ensures no contamination of the treated parts.
High-quality, durable silico-sodo-calcium glass microbeads (free of free silica) are manufactured from recycled glass in France.
-
Iron Silicate
€16.75 HTSandblasting abrasive for free-blast or airblast applications, ideal for cleaning and stripping metal and stone/concrete, removing scale, rust, old paint coats and various dry impurities.
-
Plastic Media Type II
€189.75 HTSandblasting abrasive used for overpressure gumming in sandblasting cabinets.
Type II is the most widely used and versatile media for surface treatment. It has an average hardness within the range of thermoformed plastic media. It can be used for surface treatment in dry or wet environments.
-
Plastic Media Type III
€189.75 HTSandblasting abrasive used for overpressure gumming in sandblasting cabinets.
Type III is a melamine-based thermoformed plastic media. Melamine is the most aggressive and hardest of the thermoformed plastic media (6 times more aggressive than urea - type II).
It must therefore be chosen carefully to avoid damage to delicate materials. It can be used for surface treatment in both dry and wet environments.
-
Round grit - Stainless steel microbeads
€247.50 HTRound stainless steel shot is produced by atomizing Cr Ni Stainless Steel. After various phases to obtain round pellets, precise sieving is carried out.
Its austenitic microstructure offers great durability, making it ideal for surface preparation and finishing. Its stainless properties make this product the perfect option for cases where ferrous contamination must be avoided.
Suitable for pressurized air and turbine blasting processes. It allows for better corrosion resistance and clean, bright finishes. The chemical composition of this round shot corresponds to austenitic stainless steel, which is a class of stainless steel commonly used due to its corrosion resistance and good formability.
-
Round Shot - Microbeads Steel
€151.25 HTThe technology used for the production of high-carbon steel shot is the most advanced in the world. We offers shot that meets international SAE standards.
This results in a very high-quality martensitic angular shot. Continuous quality control, combined with cutting-edge production processes, optimizes the shot's lifespan and cleaning efficiency.
-
RUGOS 50/80 Sandblasting Sand
Rugos 50/80 sandblast sand, 25kg bag.
Product unavailable, see article SC06 for equivalent abrasive.
-
Sand Archifine N°6 (25kg)
"Archifine" sandblasting sand N°6, the 25 kg bag
Out of stock: see equivalent product Scorex SC06 -
Sodium bicarbonate
€36.75 HTSoft blasting abrasive, ideal for open-air blasting to remove graffiti or stripping sensitive parts.
-
Stainless Steel Shot
€280.00 HTStainless steel shot is obtained through melting, crushing, and sieving of Cr stainless steel. The high chromium content provides excellent resistance to corrosion and use. It is an abrasive that offers great durability and recyclability due to its high resistance. Recommended for surface cleaning, removal of paints and coatings, and creating surface roughness for treatments that must be free of ferrous contamination. Ideal for the treatment of stainless steel, galvanized steel, and aluminum.
-
Steel Shot
€93.75 HTHigh-quality martensitic angular steel shot for shot blasting and sand blasting.
-
Vegetable Abrasive
€68.75 HTAbrasive for sandblasting, stripping or other impact surface treatments. This sandblasting abrasive is made from agricultural by-products such as walnut shells, pine nuts and fruit pits.
-
White fused alumina - White Corundum
€126.00 HTWhite corundum is a high-purity, extremely hard aluminum oxide used as an angular abrasive. It is free of impurities and is suitable for applications where iron oxide is not present, as it is non-ferrous.