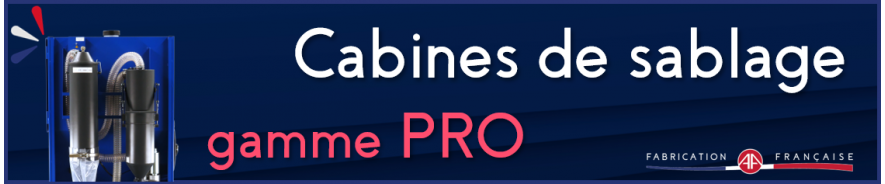
PRO Range
-
DS 1000 - Sandblasting cabinet
DS type bag cabins are professional sandblasting machines operating with a vacuum system. That is, the abrasive is projected via a venturi effect created inside the tungsten carbide nozzle .
The cyclone at the rear of the PRO series machines allows the abrasive to be sorted. Dust is discharged into the dust bag at the back of the sandblaster while larger grains of abrasive are reused.
(Price: contact us)
-
DS 1500 - Sandblasting cabinet
The DS1500 sandblasting machines are the largest machines in the PRO range.
The operating mode of these cabins is the same as for the other DS type machines: the abrasive is projected thanks to the venturi system of the tungsten carbide nozzle .
It is then separated from the dust; The dust is discharged into the recovery system integrated into the baghouse, and the pure abrasive is recycled and reinjected into the nozzle.
(Price: contact us)
-
DS 600 - Sandblasting cabinet
The DS600 vacuum blast cabinets, are reserved for very small parts and is a space-saving machine.
Its vacuum system projects the abrasive thanks to a venturi effect created inside the tungsten carbide nozzle .
The cyclone at the back of the blast cabinet is used to sort out the dust to be evacuated and the abrasive grains that can be reused.
(Price: contact us)
-
DS 700 - Sandblasting cabinet
The DS vacuum bag cabins use the same principle as all vacuum machines: a venturi system inside the tungsten carbide nozzle is used to project the abrasive onto the sandblasted workpiece.
The healthy abrasive is then separated from the dust in the cyclone at the back of the blast cabinet. The dust is collected in the collection bag and the abrasive is redirected to the nozzle.
(Price: contact us)
-
PS 1000 - Sandblasting cabinet
The PS 1000 combines the small footprint advantage with the productivity of a pressure boosting machine. The overpressure blasting means that the abrasive tank is pressurized and offers a 3 to 5 times higher yield compared to the vacuum.
Equipped with a cyclone at the rear of the machine, the PRO range allows the abrasive to be sorted. Dust is discharged into the dust bag at the back of the sandblaster while larger grains of abrasive are reused.
(Price: contact us)
-
PS 1500 - Sandblasting cabinet
The PS1500 works with an abrasive tank that is pressurized for blasting with 3 to 5 times higher yields compared to the vacuum system.
The recycling cyclone allows the separation of dust from the abrasive. The waste is then discharged into the dust collection bags and the recycled abrasive is resprayed.
(Price: contact us)
-
PS 700 - Sandblasting cabinet
The PS 700 blast cabinet combines the small footprint advantage with the productivity of a pressure boosting machine. The overpressure blasting means that the abrasive tank is pressurized and offers a 3 to 5 times higher yield compared to the vacuum.
Equipped with a cyclone, these sandblasting machines can sort the abrasive in order to separate dust and healthy abrasive grains. These are then reprojected.
(Price: contact us)
Our PRO range of blast machines are vacuum or overpressure sandblasters perfect for standard use.
Through this range, ARENA offers easy-to-use and robust sandblasting cabinets suitable for moderate use.
How do these sandblasting machines work?
PRO cabs are divided into two categories: vacuum and pressure machines.
Vacuum cabinets work via the suction of abrasive at the base of the hopper and a venturi effect created inside the machine's carbide nozzle. The abrasive is first sucked up and then projected by the nozzle onto the workpiece. Vacuum systems are simple to set up and inexpensive. This is the system that most bag blasting cabinets are equipped with.
Within this PRO range, the vacuum cabins are the DS type machines.
The other type of spray is the abrasive spray through an overpressure system. It is totally different from the vacuum projection. Here, the grains are no longer sucked up to be sprayed, they are propelled by compressed air from the abrasive tank. The abrasive tank is pressurized and when the sandblasting pedal is pressed, the abrasive is propelled through the nozzle which further accelerates the blasting speed. In this range, the pressure machines are the reference machines PS. Good to know: the overpressure spraying system offers 2 to 3 times more efficiency than a vacuum system.
What are the advantages of this range?
These sandblasters are equipped with a ventilation module integrating a cyclone for dedusting the abrasive allowing it to be cleaned continuously. This system provides better user comfort and abrasive savings.
The abrasive and dusty air are sucked in from the bottom of the hopper and arrive at the top of the cyclone, separating the abrasive from the dust. Fine abrasive grains and dust are sucked from the top of the cyclone to the second module containing the filter cartridge. The fine dust is then stored in the cartridge and each time the foot pedal is pressed, a pneumatic shock cleaning is carried out. The dust is then collected in the plastic bag at the bottom of the filter cartridge. As for the large grains of intact abrasives that have not been damaged by their first spray, they are too heavy to be sucked into the filter cartridge. They then fall directly back into the centre of the cyclone in the reserve of pure abrasive from which the abrasive will be drawn to be projected.
The advantage of the PRO range therefore lies in its abrasive recycling cyclone; It significantly reduces abrasive consumption, but also preserves the components of the cabinet and contributes to a cleaner, less dusty sandblasting environment.
Which compressor for these sandblasting booths?
Our sandblasting machines all need a compressed air supply provided by a compressor.
Vacuum machines consume less compressed air than pressurized booths because of their abrasive spraying medium requiring less compressed air.
Thus, our DS vacuum cabs will be satisfied with a compressor between 2.5 and 7 horsepower for the largest nozzle diameter.
PS-booster machines, on the other hand, require a compressor between 7 and 15 horsepower. Due to their means of spraying, these machines require more compressed air flow. Indeed, on these machines the grains are propelled through the nozzle thanks to the compressed air as seen above.
Which abrasive for sanding?
There are 2 types of abrasives: lost abrasives and recyclable abrasives.
The abrasives to be used in the blasting cabinet are recyclable abrasives; They are intended to be recycled and projected several times before they become unusable.
Within these recyclable abrasives, there are 3 types of abrasives, each with its own use:
Angular abrasives are made to tear the material from the workpiece; These are the most aggressive abrasives. They are generally used to remove rust from any metal part. The most well-known angular abrasives are corundum; There are brown corundum, and white corundum. Their technical characteristics allow them to be suitable for most sandblasting needs.
The second type of abrasive is spherical abrasives. They are most often used for finishing treatment of parts. Their rounded shape makes the pieces "shine" and gives them a particularly aesthetic appearance. The most commonly used microbeads are made of glass, but there are also ceramic or metal beads.
The third category is scrub abrasives, which are used to clean without attacking the substrate. Most of the time, abrasives such as plastic media are recommended for the treatment of fragile parts
After purchase
After the purchase of your cab, we remain present to help and guide you throughout the use of your ARENA machines.
All spare parts or consumables are in stock all year round; We respond to each email within 24 hours and delivery is done within 24 to 48 hours.
ARENA sleeve cabins are all manufactured in our workshop in Marquette-lez-Lille in the north of France.
Created more than 40 years ago, the ARENA brand is the leading brand in France in the field of sandblasting.
Our sandblasting machines are all made with quality elements that come from the European Union.
The cabins arrive in one piece, on pallets, no additional assembly to be done; an air and electricity supply and voila, your machine is ready for use!