Industrial Sandblasting Cabinets
EXPERT Range
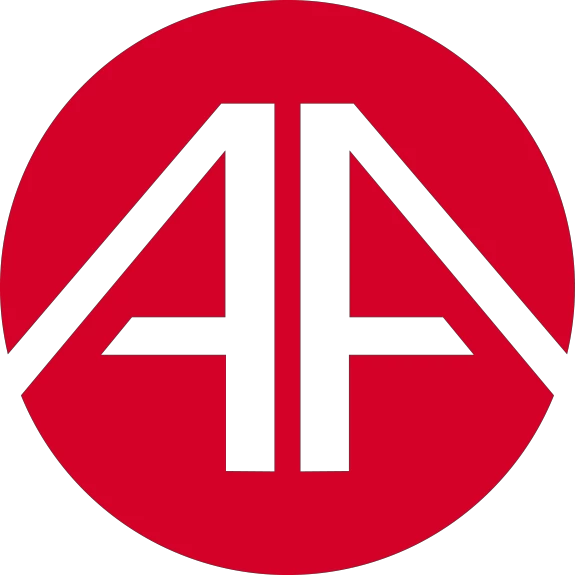
Powerful
Intensive use and complete customization of each cabin
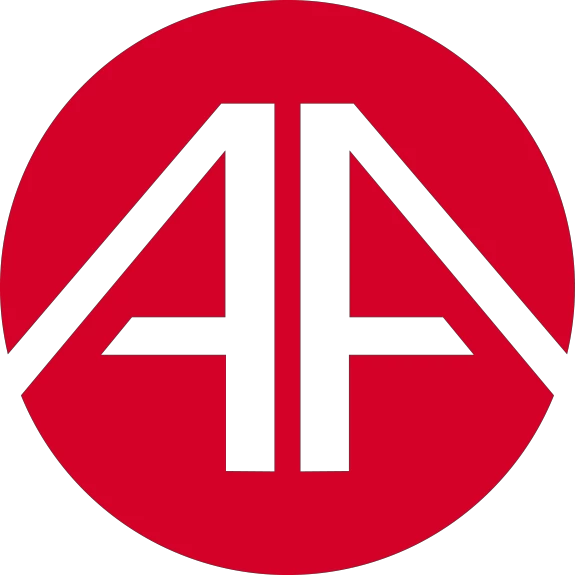
Robusts
Long-term investment thanks to robust design and easy maintenance
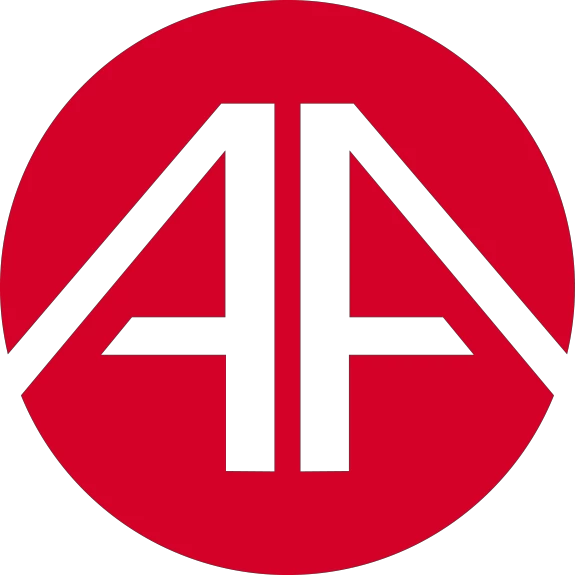
Compacts
The best and most compact sandblasting cabinets on the market
Sandblasting cabinets
EXPERT range
Powerful
Intensive use and complete customization of each cabin
Robusts
Long-term investment thanks to robust design and easy maintenance
Compacts
The best and most compact sandblasting cabinets on the market
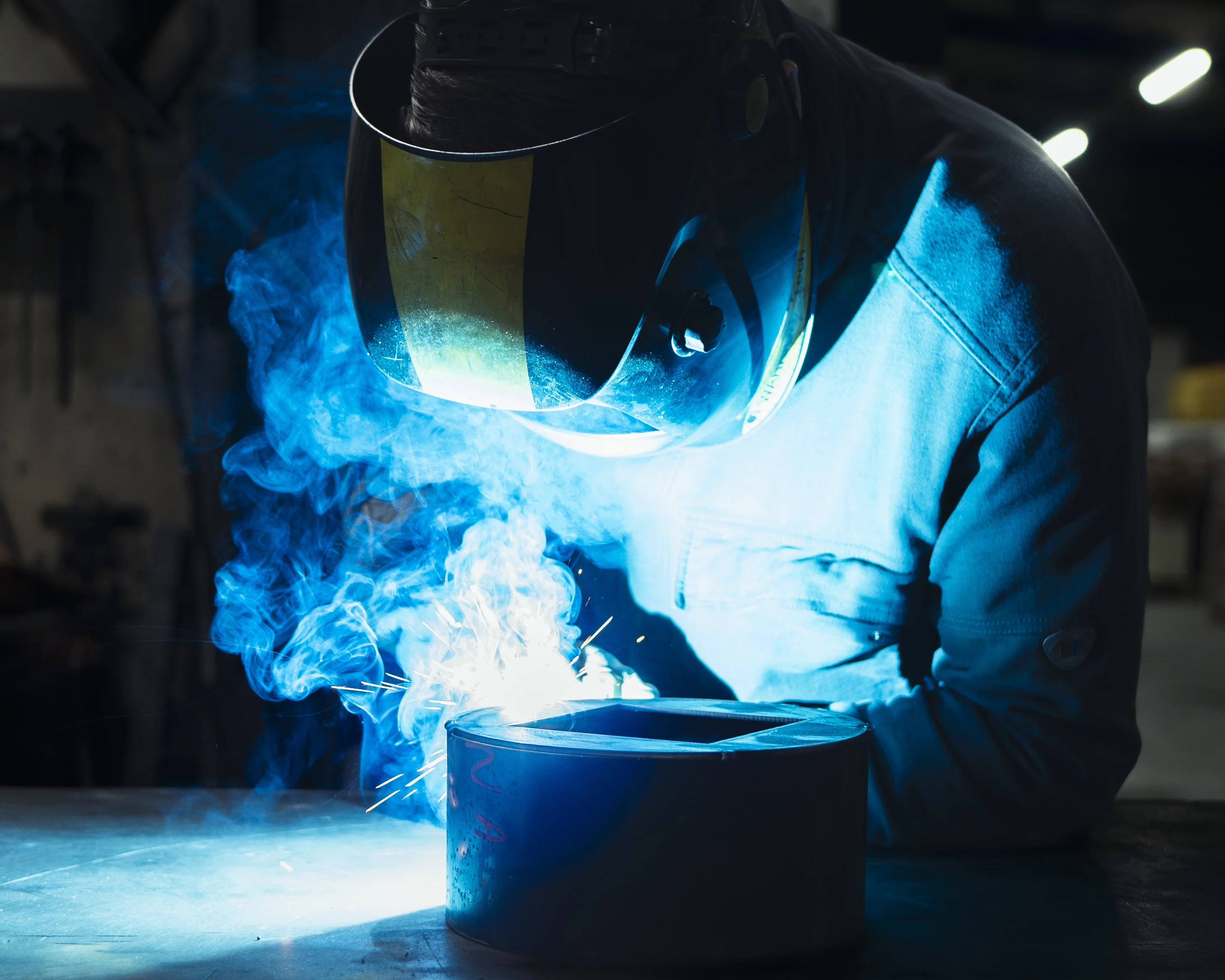
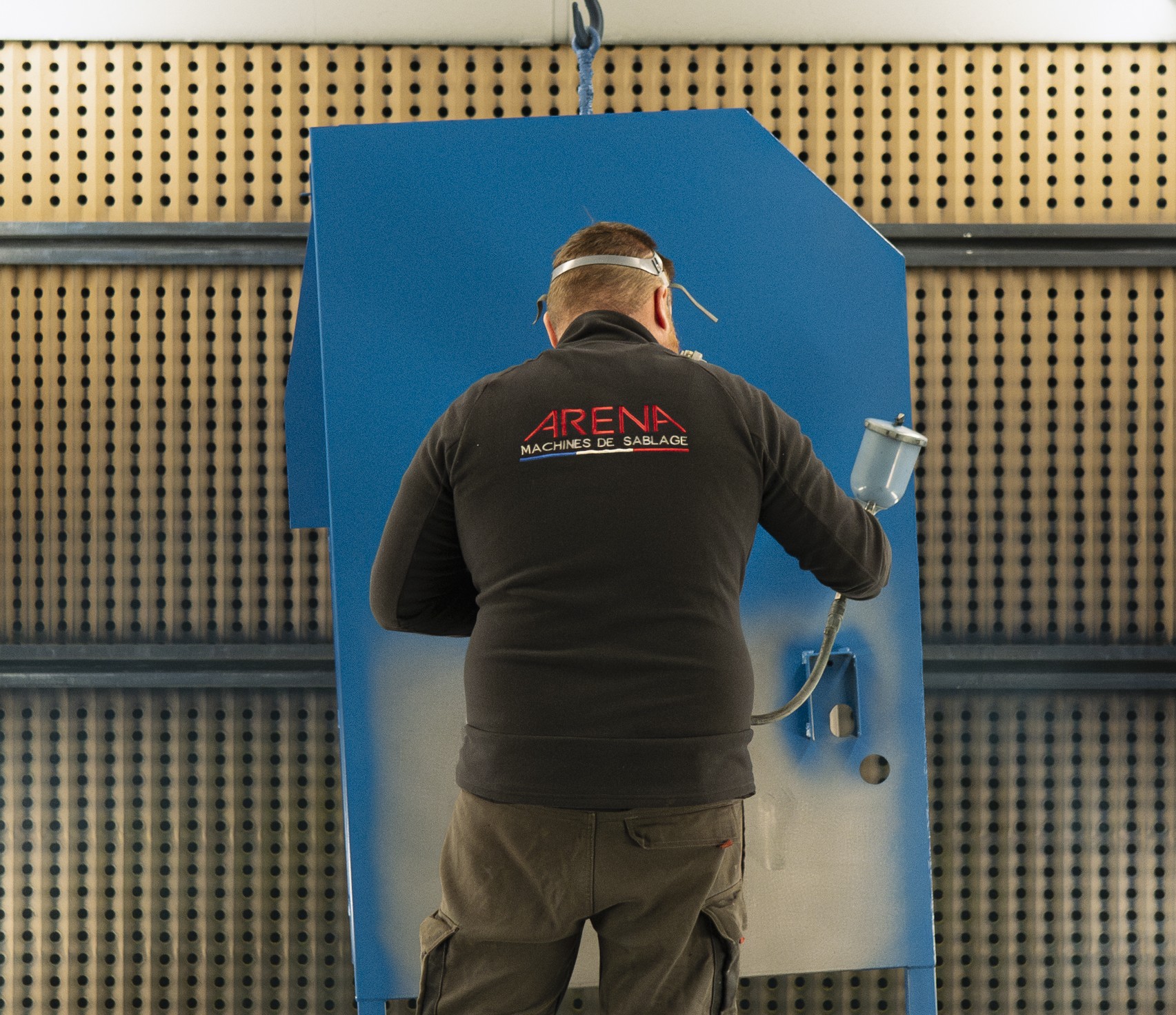
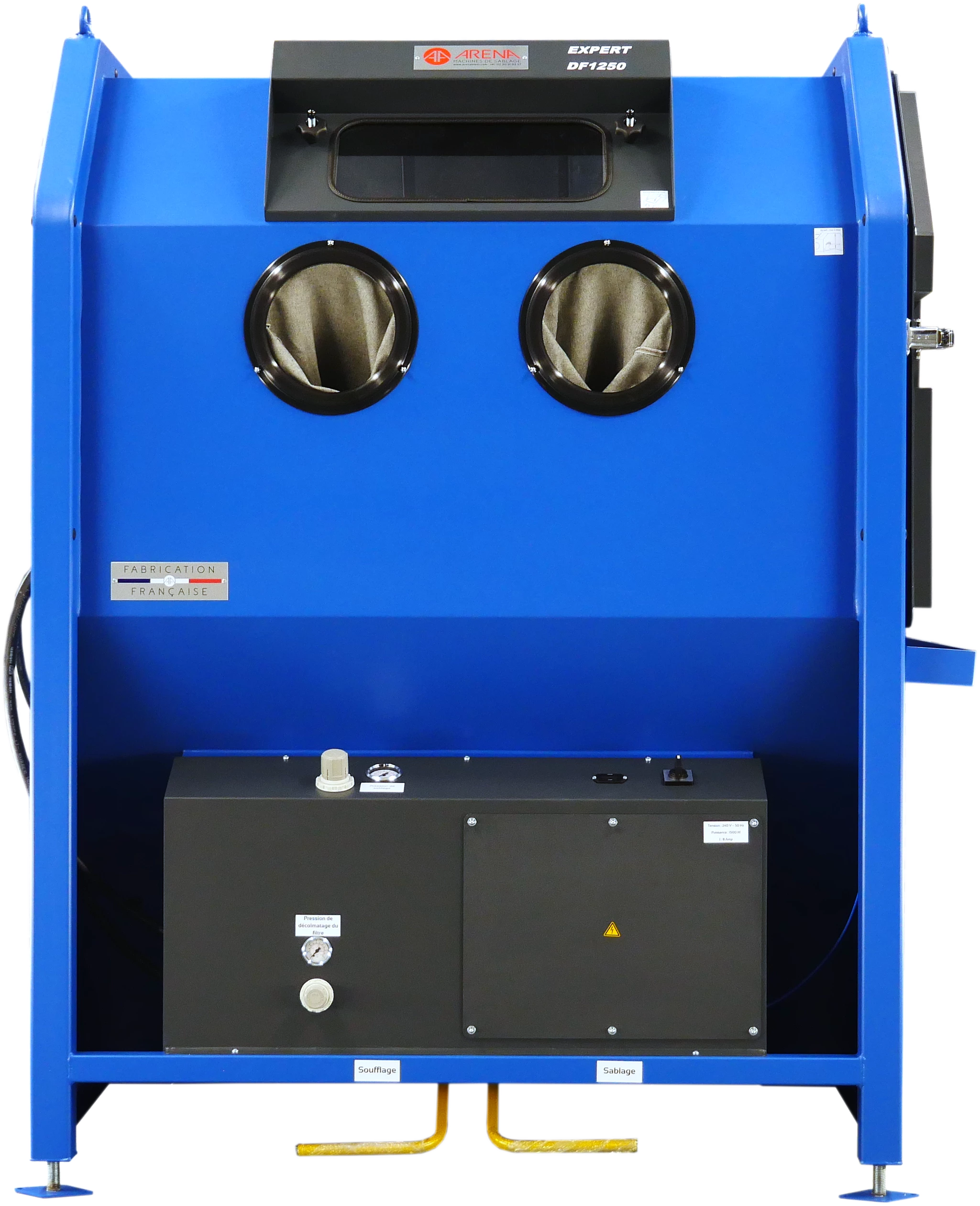

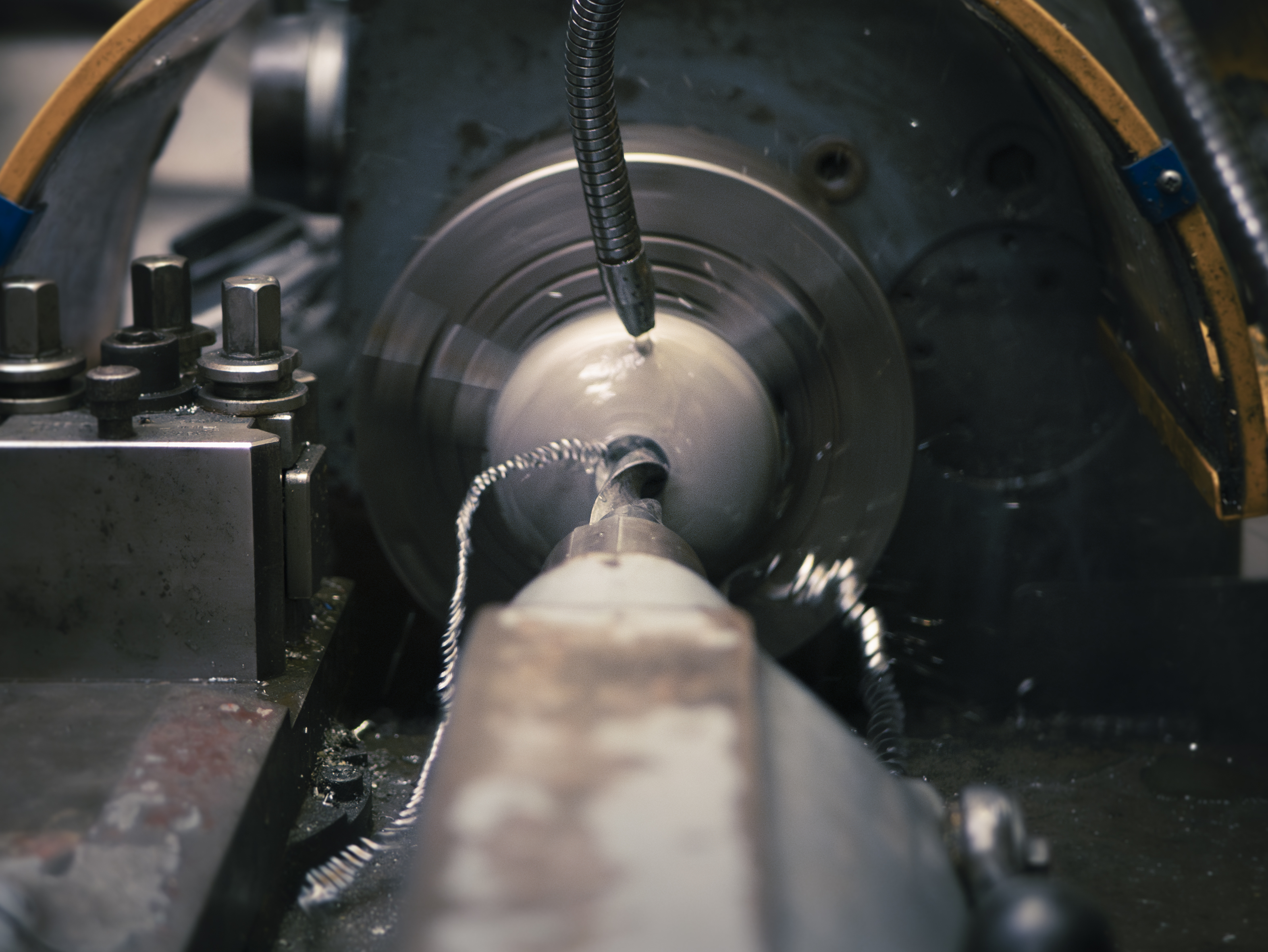
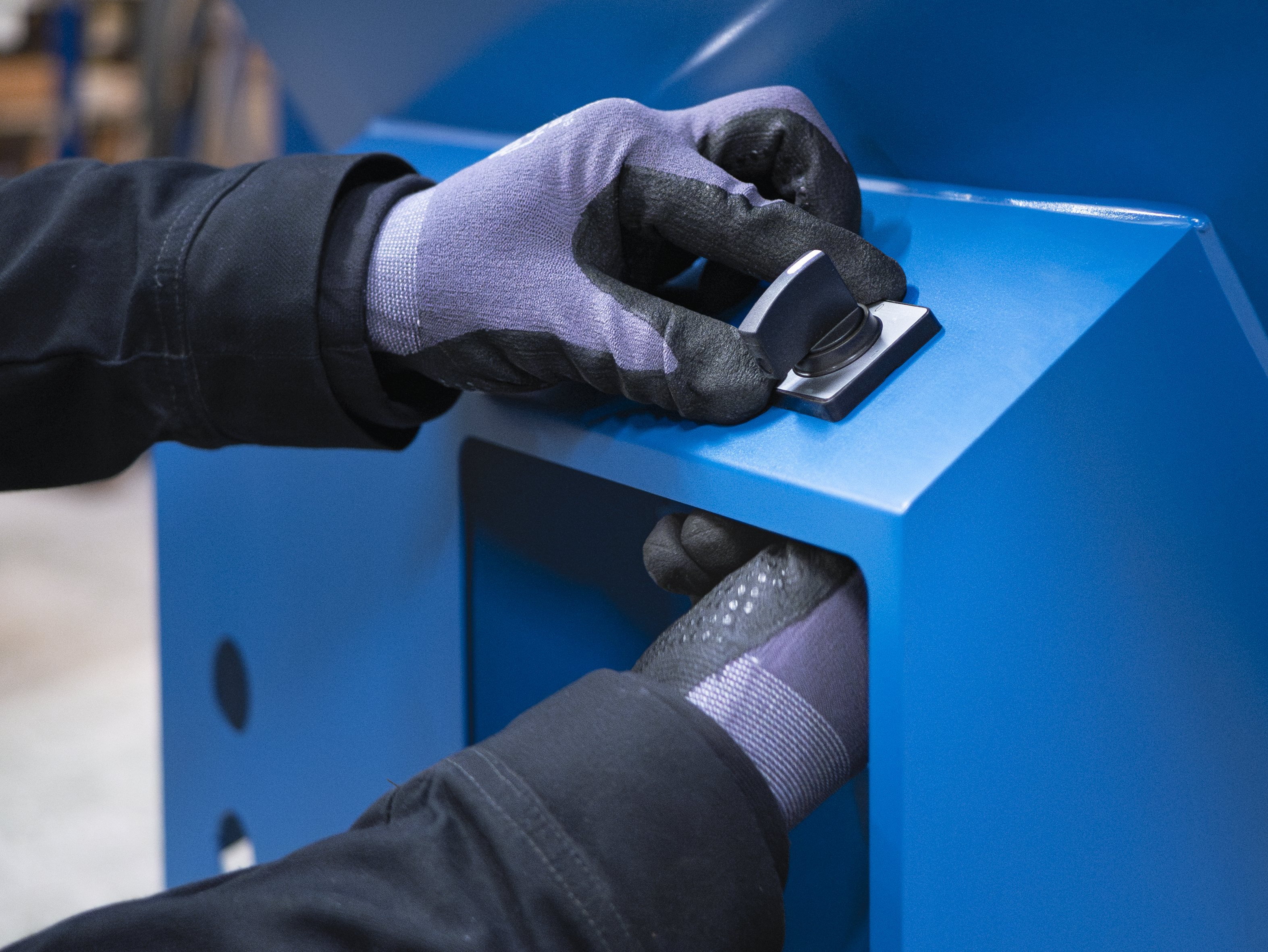
The best industrial sandblasting cabinet
- Industrial cabinet with reinforced sheet metal hoops and lifting rings
- 100% sealed machines with closed abrasive recycling circuit
- Cyclonic removal of abrasive dust for greater surface treatment precision
- Automatic filter cleaning by pneumatic shock with pressure adjustment
- Highly resistant blasting nozzle:- boron carbide for PF (+750h use)- tungsten carbide for DF (+300h use)
- Coarse dirt retention screen
- Side-channel suction turbine- 1500 W (210 m3/h) for overpressure cabins- 800 W (140 m3/h) for DF 700
- Denim sleeves and high-resistance LATEX gloves for safety and working comfort
- Compressed-air blowgun with pedal control
- Dust filtration with a 5 µm filter cartridge
- Excellent in-cab visibility thanks to 2 x 15 W LEDs and high dust extraction
The best of the sandblasting cabinet
- Industrial cabinet in reinforced sheet metal with hoops and lifting rings
- 100% sealed machines with closed abrasive recycling circuit
- Cyclonic removal of abrasive dust for greater surface treatment precision
- Automatic filter cleaning by pneumatic shock with pressure adjustment
- Highly resistant blasting nozzle:- boron carbide for PF (+750h use)- tungsten carbide for DF (+300h use)
- Coarse dirt retention screen
- Side-channel suction turbine- 1500 W (210 m3/h) for overpressure cabins- 800 W (140 m3/h) for DF 700
- Denim sleeves and high-resistance LATEX gloves for safety and working comfort
- Compressed-air blowgun with pedal control
- Dust filtration with a 5 µm filter cartridge
- Excellent in-cab visibility thanks to 2 x 15 W LEDs and high dust extraction
TRIPLE air/dust/abrasive flow management module designed by ARENA BLAST
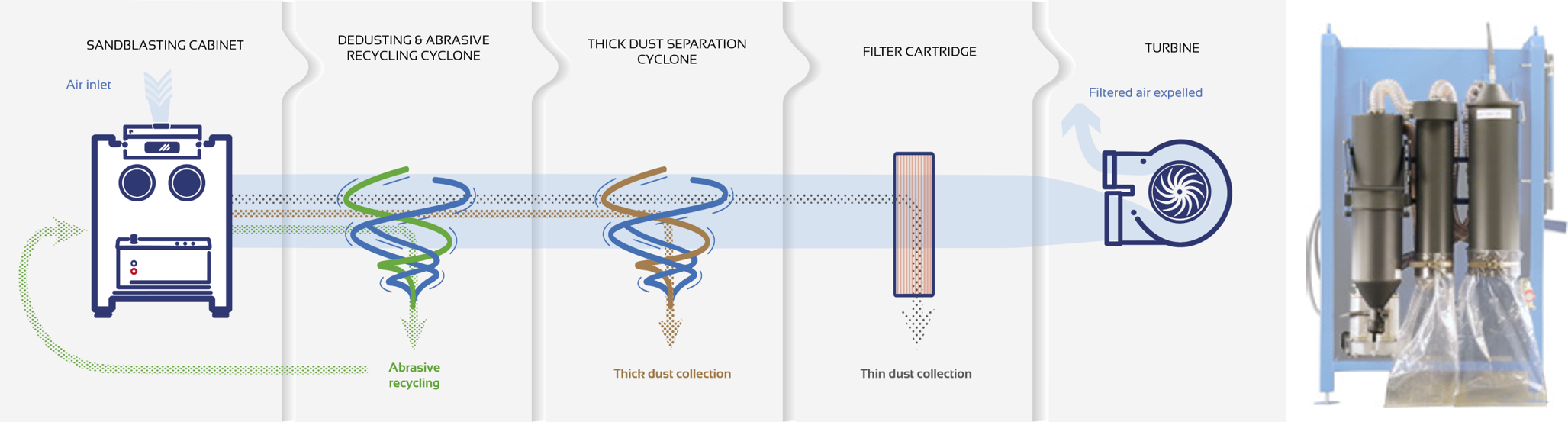
Multiple & precise settings
- Filter cleaning pressure
- 0-8 bar blasting pressure regulator with pressure gauge
- Air/abrasive mixture setting
- Cabin height - Adjustable from + to - 50 mm
- Drain and change abrasive in 5 minutes
- Intuitive replacement of main wear items - Gloves, Glasses, Filters, Nozzles - without special tools
More than 30 standard options and adaptations on request
The EXPERT range of blast cabinets is available with
with 2 abrasive projection systems
SUCTION - DF
Simple to use, with easy adjustment and maintenance, this system uses the Venturi effect to project the abrasive onto the surface to be sandblasted or blasted.
The abrasive contained in the container is sucked in to be projected, so there is a double air/abrasive feed to the gun.
This system can also be used for multi-nozzles on a cabin.
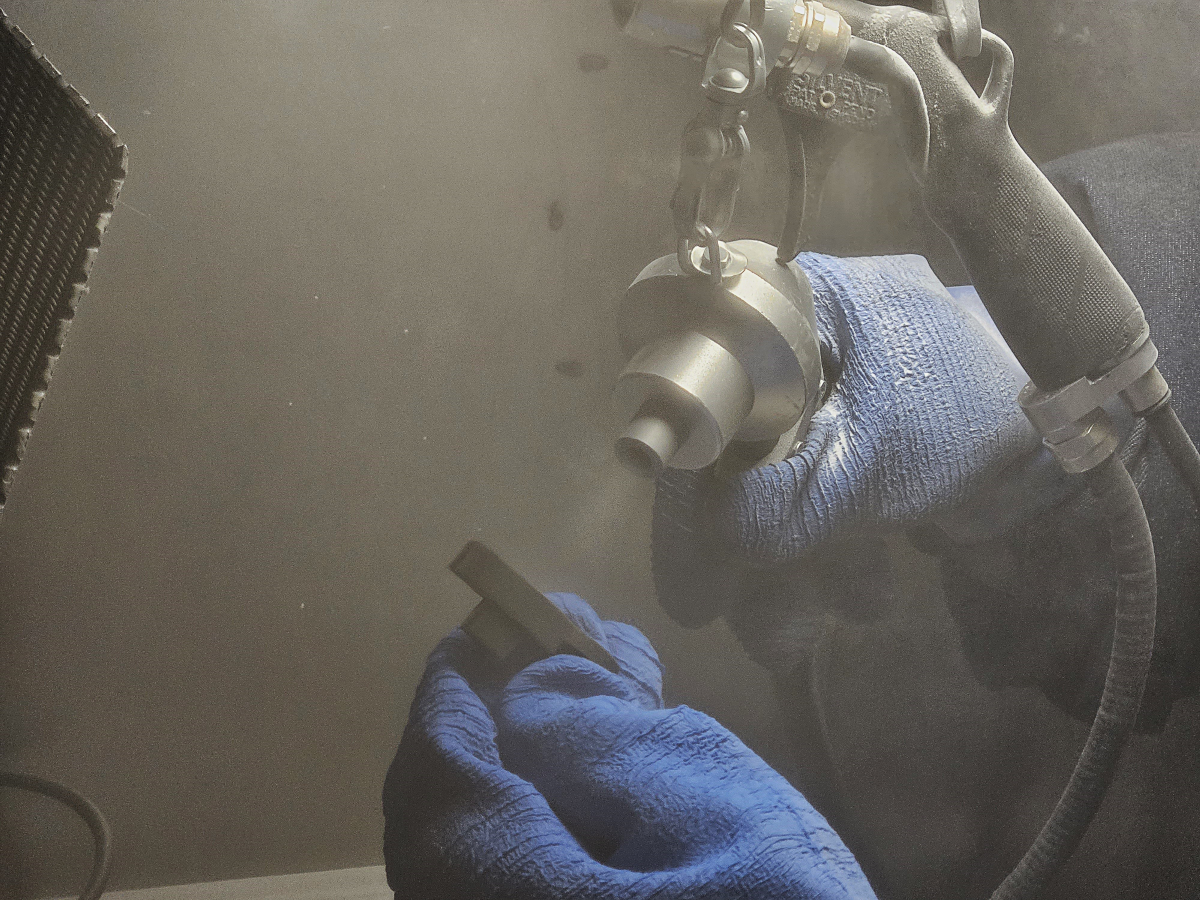
.webp)
PRESSURE - PF
This system enables higher abrasive flow rates than vacuum. It is indispensable for certain applications requiring greater blasting force (e.g. epoxy stripping).
The pot containing the abrasive is pressurized, enabling the media to be projected with much greater energy.
With more efficient, intense and powerful use, it offers yields 2 to 3 times higher than the vacuum system.
Available models and sizes
Features
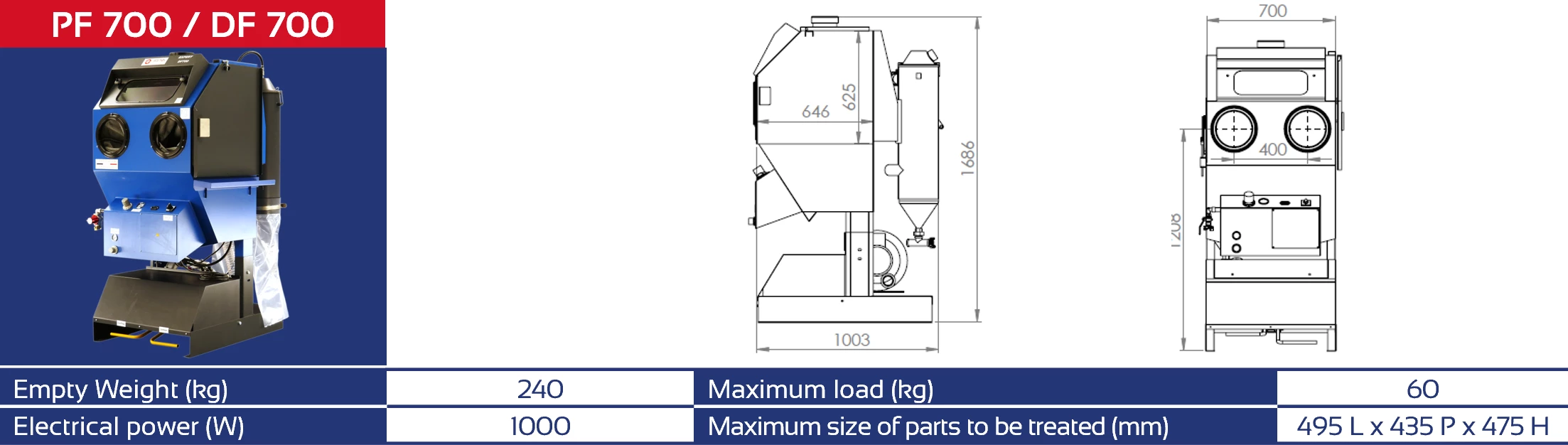
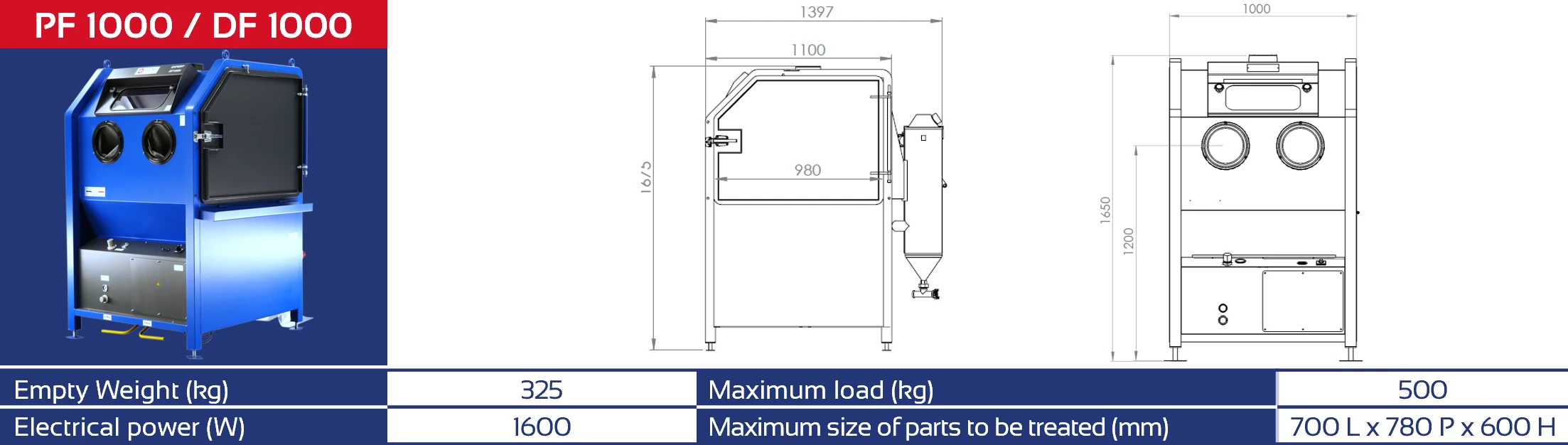
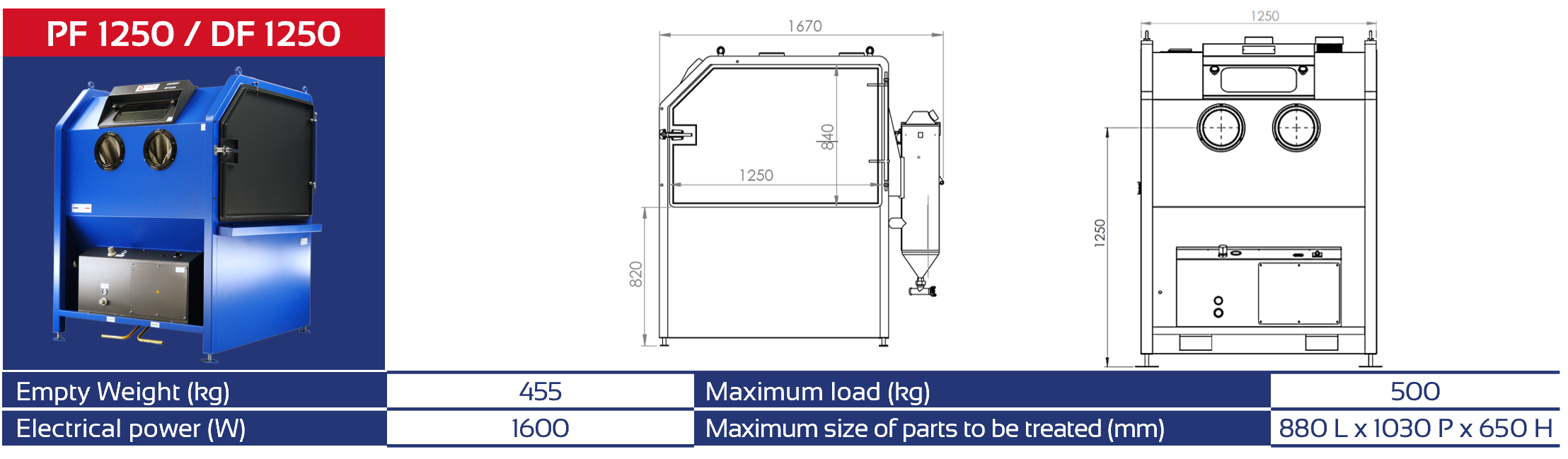
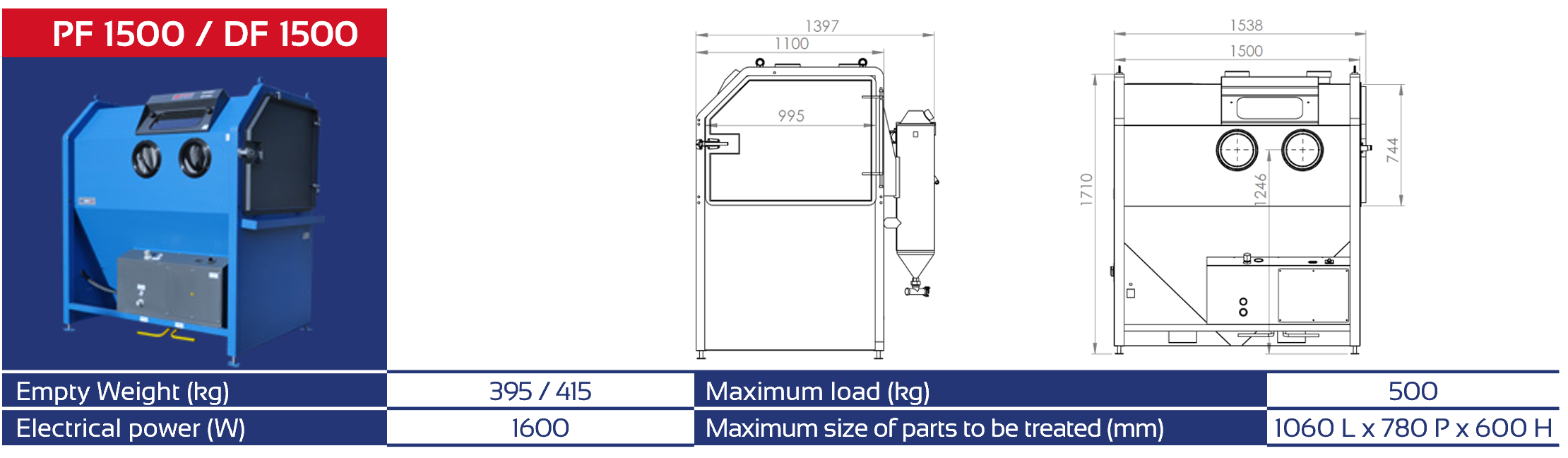
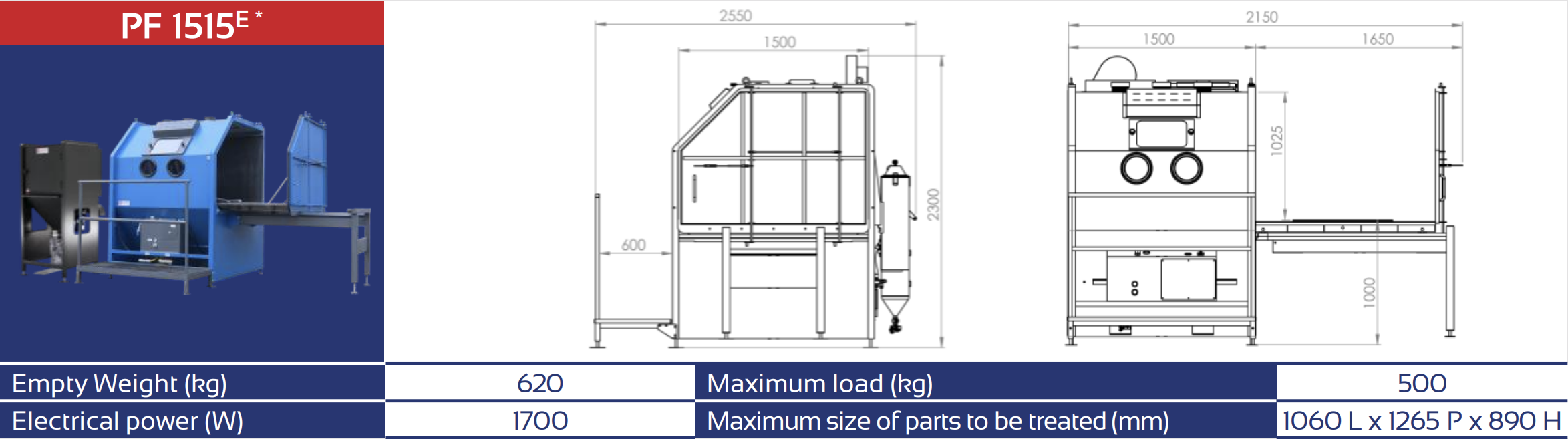
* The PF 1515 E is equipped with the reinforced loading trolley with turntable (Code CHAR 3) and a high-flow dust collector (Code DPE 750) for improved ergonomics and optimum suction and sandblasting performance.
CHOOSING THE RIGHT NOZZLE DIAMETER FOR YOUR COMPRESSOR | |||
---|---|---|---|
Pressure system | |||
Minimum compressor power | 10 ch / 7,5 kW | 15 ch / 11 kW | 20 ch / 15 kW |
Inside Ø nozzle | 4 mm | 5 mm | 6 mm |
Air consumption (for P=6 bar) | 50 m3/h | 80 m3/h | 120 m3/h |
Injection / Succion system | |||
Minimum power of piston compressor | 3 ch / 2,2 kW | 10 ch / 7,5 kW | 15 ch / 11 kW |
Minimum screw compressor power | 3 ch / 2,2 kW | 7,5 ch / 5,5 kW | 10 ch / 7,5 kW |
Inside Ø nozzle | 5 mm | 6 mm | 8 mm |
Air consumption (for P=6 bar) | 12 m3/h | 27 m3/h | 48 m3/h. |
*Excluding cumulative consumption of other machines connected to your compressed air network.
To guarantee optimum machine performance, you must ensure that the correct pipe diameters are fitted throughout your installation.